无锡sorting
PVA膜是实现偏光功能的**材料
PVA (polyvinyl alcohol)膜全称聚乙烯醇薄膜,其组分主要是碳氢氧等轻原子,因此具有高透光和高延展性等特点。将PVA膜在染色槽中染色后,其表面会均匀的富集一层碘分子(或染料分子)。未经处理的PVA分子链呈杂乱分布,此时吸附其上的碘分子(或染料分子)也杂乱分布;当PVA经外力作用拉伸后,PVA分子链延外力方向分布,此时碘分子(或染料分子)也有序分布,从而使PVA膜具备了偏光的功能。
目前市场上的偏光片可依据PVA膜上起到偏光作用的二向性分子不同来分类,主要包括金属偏光膜,碘系偏光膜,染料系偏光膜和聚乙烯偏光膜等。其中碘系偏光膜由于透光率和偏振度高,sorting,是目前应用较广的偏光膜。
3、主要产品特点及应用领域
偏光片主要性能指标包括光学特性、机械性能和可靠性三方面。光学特性主要是指偏光片的透过率、偏振度和色调等参数;机械性能主要包括偏光片的翘曲度、偏光片压敏胶的粘结强度等;可靠性则是衡量偏光片耐久性的指标,其评价方法是将偏光片放置在高温、低温、高温高湿等环境试验箱中经过一定的时间后,检查其外观和光学性能的变化。
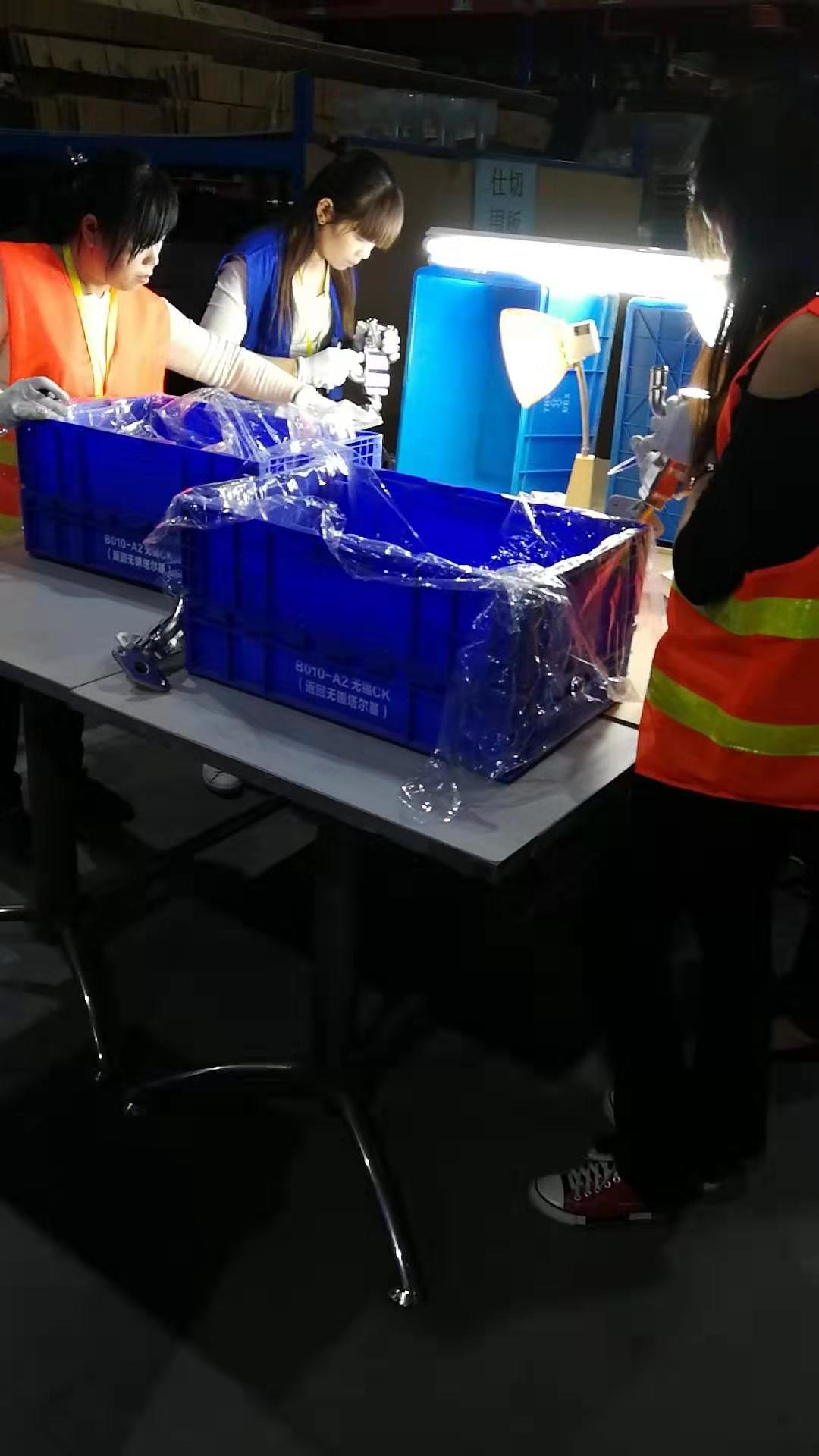
金蚂蚁返工公司 是一家专业的第三方返工公司 专业从事汽车零配件;电脑/手机零配件的外观检验,性能测试, 有经验丰富的技术带队人员50多名,有熟练的品质挑选人员300多名,我们可以及时派人到客户指定的地点、工厂、生产线或仓库进行sorting,返工服务作业,能提供24小时的服务响应。真正做到让客户无忧。 上海返工 苏州返工 无锡返工 常州返工 南通返工 南京返工
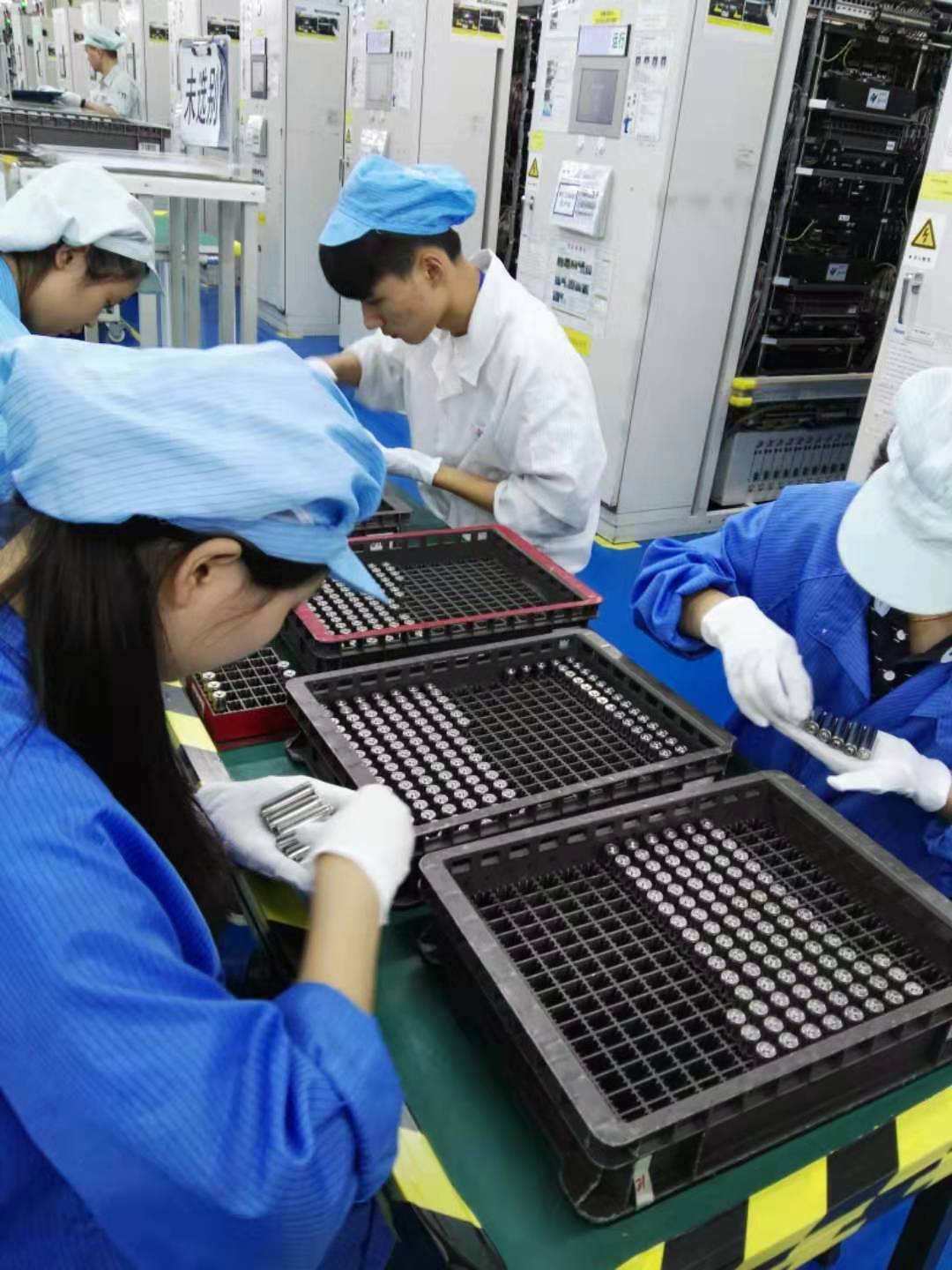
公司可提供专业检测设备,为客户解决品质突发问题并解决方案,我们的服务遵循ISO 9001:2008质量管理体系,快速响应、按客户需求提供服务,期待与您合作。
随着液晶屏幕制造的技术的发展,液晶屏幕的显示效果虽已有了大幅的提升,但液晶屏幕生产过程中出现坏点和亮点的现象还是难以避免。那么当我们在购买工业液晶屏、液晶显示器等之前到底应该如何检查液晶屏幕是否有坏点呢?下面给大家简单介绍一下检测液晶屏幕坏点有哪些。
液晶电视屏亮点分为两种:
1、亮点:亮点也是坏点的一种,这是指对应像素的三个液晶盒中只有一个或两个驱动管出现了故障,那么在黑背景下则会呈现红、绿、蓝中一种颜色的像素点;或者原来应是红、绿、蓝三色的点却呈现为白色,这些可判断为亮点,也是坏点的一种。
2、一半坏点:某个点出现在任何颜色背景下仍然呈现为纯黑或纯白的像素点即为坏点。这可能是对应像素的三个液晶盒驱动管都出现故障而导致出现坏点。
无锡sorting, 当供应商完成挑选后,作为客户还要确认的一项事宜就是挑选的结果,很多公司会将挑选的结果确认放在8D报告的数据审查里面,这里跟大家交流下挑选后的产品数据都要有哪些?首先,一共挑选出多少件不良不良品的数量会给SQE一个诊断问题的主方向,如果不良比例很高,可以确定这个问题是批量问题,并且供应商产线没有识别问题的有效措施。其次,不良品是连续生产出来的吗?如果不是连续生产出来的,那么这个问题产生的原因往往是特殊原因;如果是连续生产出来的,这个问题产生的原因往往是一般原因。再次,不良品是否有共性特征比如批次信息,工装/模穴号,产线代码,操作工关联性,分供方原材料等等。这些信息的搜**让我们逐步缩小筛查问题根本原因的范围。Sorting这活儿,说起来容易,做起来其实还是有很多道道儿的,希望大家不要忽视这个看起来技术含量很低,但实际上可以为你提供很多有价值信息的工作。
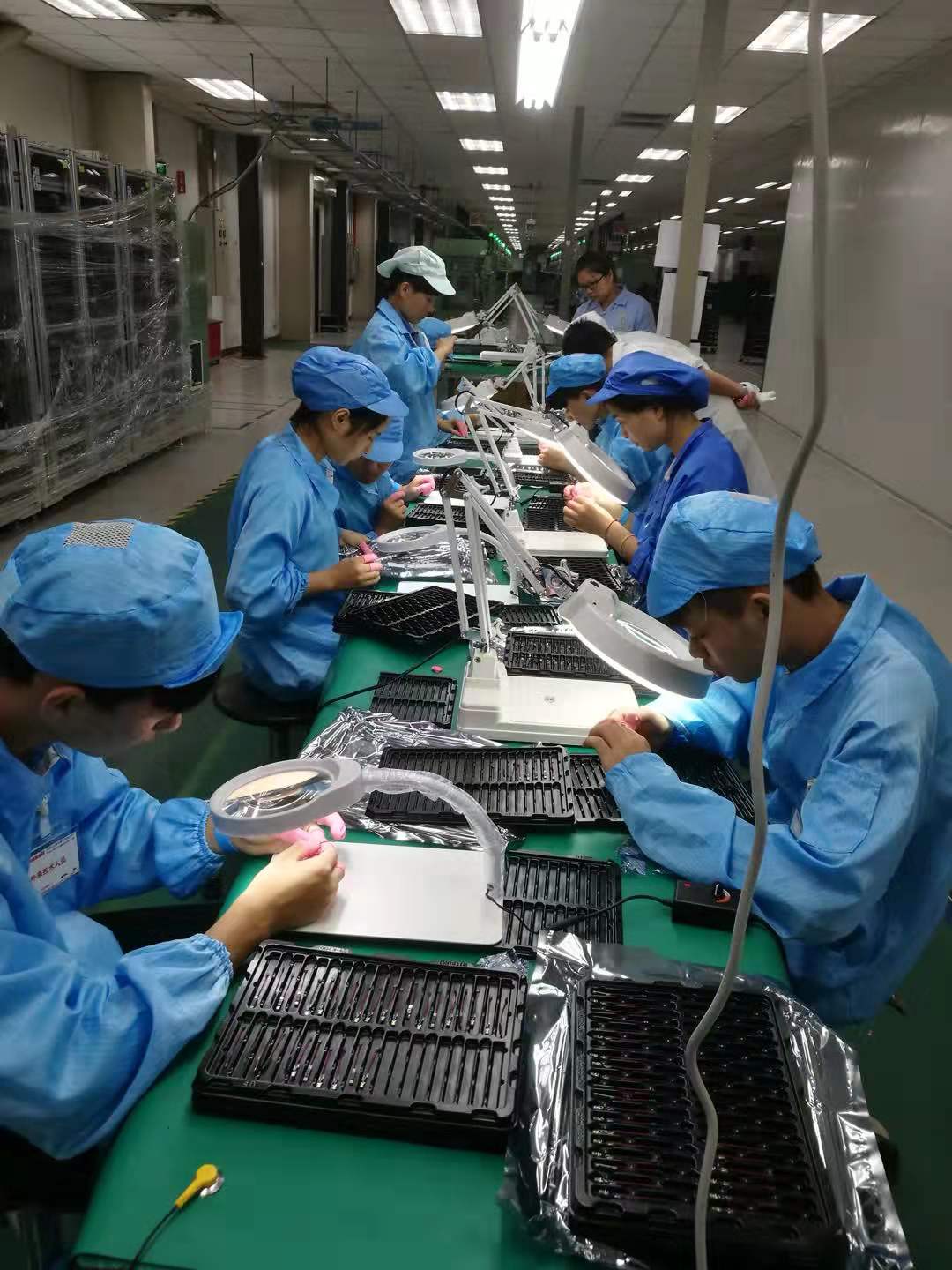
OBA检验流程事项
1. 所有转待判仓物料,需QA客诉会议或QA课长级(含)以上人员通知方可执行;
2. OBA出货检验异常→通知QC确认(QC会同产线一起)→确认NG→OBA开立异常单,隔离此批物料;如有争议,确认是否有签样和找QA复判;如复判OK,正常出货,如复判NG以不良品处理流程作业;OBA通知仓库另备一批出货,在出货紧急又无库存的情况下,非功能性不良需QA组长级确认此不良在客户端无影响,可协调OBA主管允收此批物料;功能性不良QA需报备品保理级主管,由理级主管通知方可放料;
3. 一颗料不可同时两人检验,除非是急料,出货时须分模号穴、FQC章日期;
4.不同产品不可放置同一栈板,出货检验如发现此现象,及时通知仓库分开放置,如不分开放置则不予检验;
5. 广达免验产品需有免验票方可出货,且免验票盖章要一半盖在免验票上另一半盖在箱子上,所有免验产品需一人检验,一人确认,OK后方可出货;
6. 出货海外产品,外箱J-LABLE上生产日期不可超过一个月,如有超出需通知QA且进行隔离,另所有外箱J-LABLE需刷条形码确认;
无锡sorting, 关于sorting,想跟大家分享些经验。首先,你令供应商sorting的时候,一定要有清晰的作业指导书,指导书中必须包含:OK/NOK品的文字描述,对比照片,图纸或技术文件关于不良特性的定义。其次,sorting必须定义方法,包括使用到的设备,仪器,工具。如果**通过人员目视就可以发现不良,那么必须定义目视距离,光线条件,手持零件方式和一次**多手持多少件产品。再次,关于sorting的顺序一般遵照:按照产品距离客户产线的远近,优先挑选距离客户近的产品。例如一般顺序:客户产线处 - 客户原材料仓库 - 发往客户仓库的在途品 - 供应商发货仓库 - 供应商产线(产线仍然遵守距离客户由近至远) - 供应商原材料(如果涉及)***,就是挑选完成的产品,做了什么样的标识可以让客户看到后放心地使用,一般都是有一个蓝色的醒目标签,上面标识:已挑选/Sorted.